7.1: Глава 7: Бережливе виробництво
- Page ID
- 102683
ОБ'ЄКТИВНИЙ
Після завершення цього блоку ви повинні мати можливість:
- Застосовуйте 5S в будь-якому Машинному магазині.
- Опишіть концепцію Кайдзен.
- Опишіть впровадження бережливого виробництва.
Пісне 5S:
«5S» - це метод організації робочого місця, який складається з п'яти слів: Сортувати, Встановити в порядку, Блиск, Стандартизувати та Підтримувати. Всі ці слова починаються з букви С. Ці п'ять складових описують, як зберігати речі і підтримувати новий порядок. При прийнятті рішень співробітники обговорюють стандартизацію, яка зробить процес роботи зрозумілим серед працівників. Роблячи це, кожен співробітник відчує право власності на процес.
Фаза 0: Безпека
Часто передбачається, що правильно виконана програма 5S поліпшить безпеку на робочому місці, але це помилково. Безпека — це не варіант, це пріоритет.
Фаза 1: Сортувати
Перегляньте всі предмети на робочому місці, зберігаючи тільки те, що потрібно.
Фаза 2: Випрямити
Все повинно мати місце і бути на місці. Елементи повинні бути розділені і марковані. Все повинно бути влаштовано продумано. Співробітникам не доведеться повторюватися нахилятися. Помістіть обладнання поблизу місця, де воно використовується. Цей крок є частиною того, чому lean 5s не вважається «стандартизованим очищенням».
Фаза 3: Блиск
Слідкуйте за тим, щоб робоче місце було чистим і акуратним. Роблячи це, буде легше усвідомлювати, де знаходяться речі і де вони повинні бути. Після роботи почистіть робочу область і поверніть все в колишнє положення. Утримання робочого місця в чистоті повинно бути інтегровано в повсякденне життя.
Фаза 4: Стандартизація
Стандартизуйте робочі процедури та зробіть їх послідовними. Кожен працівник повинен знати, які їхні обов'язки, виконуючи перші три кроки.
Фаза 5: Підтримуйте
Оцінювати і підтримувати стандарти. Перераховані вище кроки повинні стати новою нормою в експлуатації. Не варто поступово повертатися до старих способів. Беручи участь в новій процедурі, подумайте про способи поліпшення. Перегляньте перші чотири кроки, коли представлені нові інструменти або вимоги до виводу.
Кайдзен
Хоча процес lean 5S зосереджений на вивезенні відходів, Кайдзен зосереджується на практиці постійного вдосконалення. Як і lean 5S, Кайдзен виділяє три основні аспекти робочого місця: M uda (відходи), M ura (невідповідності) і M uri (навантаження на людей і машини). Однак поетапний процес Кайдзен більш обширний, ніж процес lean 5S.
Огляд процесу Кайдзен:
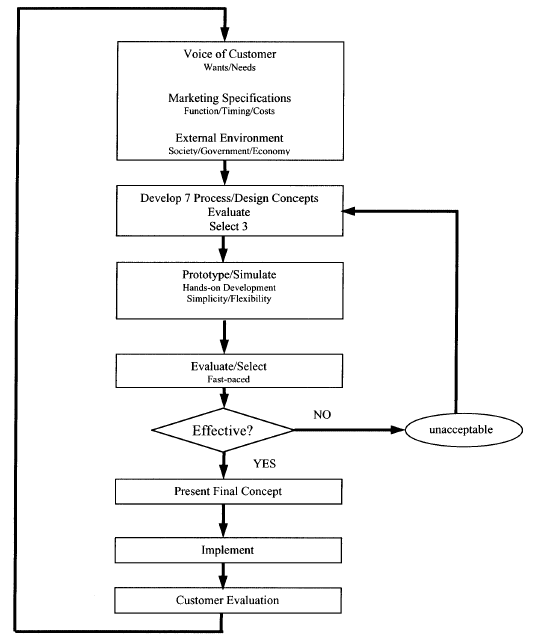
1. Визначте проблему.
2. Сформуйте команду.
3. Збирайте інформацію від внутрішніх та зовнішніх клієнтів та визначте цілі для проекту.
4. Перегляньте поточну ситуацію або процес.
5. Мозковий штурм і розглянемо сім можливих альтернатив.
6. Визначте три найкращі альтернативи з семи.
7. Імітуйте та оцінюйте ці альтернативи перед реалізацією.
8. Презентуйте ідею та пропозиції менеджерам.
9. Фізично реалізуйте результати Кайдзен та враховуйте наслідки.
Бережливе виробництво покращується з часом, тому важливо продовжувати освіту щодо підтримки стандартів. Дуже важливо змінити стандарти та навчити працівників, коли вони пред'являються новим обладнанням або правилами.
Пісний
Подумайте про відділ технічного обслуговування як про обслуговування внутрішніх клієнтів: різних відділів та працівників компанії.
Lean відрізняється від традиційної західної моделі масового виробництва, яка спирається на економію масштабу для створення прибутку. Чим більше ви зробите, тим дешевше стане товар, тим більше потенційна норма прибутку. Він заснований на прогнозах потреб клієнтів або створенні потреб клієнтів. Він має труднощі в боротьбі з незвичайними змінами попиту.
Бережливе виробництво відповідає перевіреним попитом споживачів. Потягніть обробку — замовник тягне виробництво. У масовій системі виробник виштовхує продукт на ринок, штовхає обробку.
Побудова довгострокової культури, яка зосереджена на вдосконаленні.
Повага до працівників, краще навчених та освічених, більш гнучких
Lean - це філософія, яка фокусується на наступному:
- ЗаДОВОЛЕННЯ ПОТРЕБ КЛІЄНТІВ
- Постійне, поступове вдосконалення
- Виготовлення постійно кращих продуктів
- Оцінка вхідних витрат працівників
- Беручи довгострокову перспективу
- Усунення помилок
- Усунення відходів
Відходи: використання занадто багато ресурсів (матеріали, час, енергія, простір, гроші, людські ресурси, погані інструкції)
Відходи:
- перевиробництво
- дефекти
- непотрібна обробка
- Очікування (витрачаючи час)
- Даремно витрачаючи людський час і талант
- Занадто багато кроків або пересуваннянадмірного транспорту
- Надмірний інвентар
Бережливе виробництво включає роботу з постачальниками, субпідрядниками та продавцями для потоку всього процесу.
Мета полягає в тому, щоб виробництво протікало плавно, уникаючи дорогих запусків і зупинок.
Ідея називається якраз вчасно «виробляти тільки те, що потрібно, коли це потрібно, і тільки в необхідній кількості». Процес виробництва повинен бути гнучким і швидким.
Інвентар = саме те, що вам потрібно
У масовому виробництві = про всяк випадок. Додаткові витратні матеріали та продукти зберігаються на всякий випадок, якщо вони потрібні.
Термінологія:
Спрощення процесу — процес поза потоком виробництва
Дефекти - система масового виробництва проводить перевірку в кінці виробництва, щоб виявити дефекти перед їх відправкою. Проблема полягає в тому, що ресурси вже «витрачені» на виготовлення відходів» Намагайтеся негайно запобігати проблемам, як вони трапляються, а потім запобігайте їх. Інспекція під час виробництва, на кожному етапі виробництва.
Безпека - боляче час - це витрата часу
Інформація - потрібна правильна інформація в потрібний час (занадто багато, занадто мало, занадто пізно)
Принципи:
Poka-yoke — доказ помилок, що визначають причину проблем, а потім усувають причину для запобігання подальших помилок
Помилки судження - пошук проблем після процесу
Інформативні перевірки — аналіз даних перевірок під час процесу
Перевірки джерел - перевірка перед початком процесу для запобігання помилок.
ОЗНАЧАЄ ХУДИЙ
Одним з термінів, що застосовуються до просто скорочення витрат, робота різання інтерпретації Lean є Mean Lean. Часто сучасні менеджери думають, що вони роблять худий, не розуміючи важливості працівників та довгострокових відносин.
Надійність орієнтоване обслуговування
Технічне обслуговування, орієнтоване на надійність, - це система для розробки економічно ефективної програми технічного обслуговування. Це може бути детальний складний, комп'ютерний, статистично керований, але за своїми основами він досить простий. Його ідеї можуть бути застосовані до проектування та експлуатації системи PM, а також можуть керувати вашим навчанням, коли ви виконуєте технічне обслуговування, усунення несправностей, ремонт та енергетичні роботи.
Це основні принципи RCM. Ці дев'ять основних понять:
- Відбуваються збої.
- Не всі збої мають однакову ймовірність.
- Не всі збої мають однакові наслідки.
- Прості компоненти зношуються, складні системи виходять з ладу
- Хороше обслуговування забезпечує необхідну функціональність для найнижчих практичних витрат
- Технічним обслуговуванням можна домогтися тільки властивої конструкції надійності обладнання
- Непотрібне обслуговування забирає ресурси від необхідного обслуговування
- Хороші програми технічного обслуговування піддаються постійному вдосконаленню.
Технічне обслуговування складається з усіх дій, що вживаються для забезпечення того, щоб компоненти, обладнання та системи забезпечували свої передбачувані функції, коли це потрібно.
Система RCM заснована на відповіді на наступні питання:
1. Які функції і бажані стандарти роботи обладнання?
2. Якими способами він може не виконувати свої функції? (Які найімовірніші збої? Наскільки ймовірний кожен тип поломки? Чи будуть очевидні невдачі? Чи може це бути частковий збій?)
3. Що викликає кожен збій?
4. Що відбувається, коли відбувається кожен збій? (Який ризик, небезпека тощо?)
5. Яким чином кожна невдача має значення? Які наслідки повної або часткової відмови?
6. Що можна зробити, щоб передбачити або запобігти кожній невдачі? Скільки буде коштувати передбачити або запобігти кожній невдачі?
7. Що робити, якщо не вдається знайти відповідне проактивне завдання (дії за замовчуванням) (завдання не може бути доступним, або це може бути занадто дорогим для ризику)?
Обладнання вивчається в контексті того, де, коли і як воно використовується
Всі дії з технічного обслуговування можна класифікувати на одну з наступних категорій:
- Коригувальне обслуговування - Відновлення втраченої або деградованої функції
- Профілактичне обслуговування - мінімізує можливість виходу функції з ладу
- Альтернативне технічне обслуговування - Усунути незадовільний стан шляхом зміни конструкції системи або використання
У категорії профілактичних робіт всі виконані завдання можна охарактеризувати як належність до одного з п'яти (5) основних типів завдань:
- Умова спрямована - поновіть життя на основі виміряного стану порівняно зі стандартом
- Час спрямований - поновіть життя незалежно від стану
- Пошук несправностей — Визначте, чи сталася несправність
- Обслуговування — додавання/поповнення витратних матеріалів
- Змащення - масло, мастило або інше змащення
Ми робимо технічне обслуговування, тому що вважаємо, що надійність обладнання погіршується з віком, але що ми можемо зробити щось для відновлення або підтримки початкової надійності, яка себе окупає.
RCM орієнтований на надійність. Його мета полягає в підтримці властивої системі або конструкції обладнання надійності, визнаючи, що зміни властивої надійності можуть бути досягнуті лише за рахунок конструктивних змін. Треба розуміти, що обладнання або систему необхідно вивчати в тій ситуації, в якій воно працює.
Впровадження бережливого виробництва
Проаналізуйте кожен крок початкового процесу перед внесенням змін
Бережливе виробництво основна увага приділяється зниженню витрат та збільшенню обороту та усунення діяльності, яка не додає вартості виробничому процесу. В основному те, що робить бережливе виробництво - це допомогти компаніям досягти цільового виробництва, а також інші речі, впроваджуючи інструменти та методи, які легко застосовувати та обслуговувати. Те, що ці інструменти та методи роблять, це зменшення та усунення відходів, речей, які не потрібні у виробничому процесі.
Інженери-виробники вирішили використовувати шестисигмну методологію DMAIC (проектування, вимірювання, аналіз, вдосконалення, контроль) - у поєднанні з бережливим виробництвом - для задоволення вимог замовника, пов'язаних з виробництвом труб.
Інженерам-виробникам було доручено розробити новий технологічний макет лінії виробництва труб. Цілями проекту були:
- Покращена якість
- Зниження брухту
- Доставка до місця використання
- Менші розміри партії
- Реалізація тягової системи
- Кращий зворотний зв'язок
- Збільшення виробництва
- Індивідуальна відповідальність
- Зниження НЗВ
- Гнучкість обіду
Перш ніж вносити зміни, команда аналізує кожен крок у оригінальному макеті процесу виробничої лінії труб.
1. Там намагаються зрозуміти початковий стан процесу, визначити проблемну область, непотрібний крок і не додану вартість.
2. Після відображення процесу команда lean зібрала дані зі стенду Ради з огляду матеріалів (MRB) для вимірювання та аналізу основних типів дефектів. Щоб краще зрозуміти процес, команда також провела дослідження часу протягом 20 днів виробничого циклу.
У початковому стані трубопровід складався з одного оператора і чотирьох операцій, розділених на дві станції великим столом за допомогою системи поштовху. Таблиця виступала роздільником між другою і третьою операцією.
Першою виявленою проблемою була неврівноважена лінія. Перша станція використовувалася близько 70% часу. Оператори на другій станції витрачали багато часу на очікування між часом циклу. Об'єднавши одну і дві станції, стало очевидним місце для вдосконалення щодо індивідуальної відповідальності, контролю інвентаризації оператором та негайного зворотного зв'язку, коли виникла проблема. Дослідження часу та планування кафедри відображають ці висновки.
Друга проблема була визнана. Через технологічний потік швидкість виробництва не дозволила виконати виробничий графік з двома станціями. Оскільки оператори втратили сліди машинних циклів, машини чекали уваги оператора. Оператори також намагалися проштовхнути деталі через першу станцію - вузьке місце в процесі, а потім продовжували виготовляти деталі на останніх двох операціях. Як правило, тривалі тиражі WIP накопичуються, і проблеми з якістю не були виявлені, поки не було вироблено велику кількість дефектних штук.
Первісні державні дані були взяті за останні 20 днів до зміни. Команди аналізують кожен крок в оригіналі та вносять зміни. Висновки дослідження часу на початковому процесі послужили основою для скорочення часу циклу, балансування лінії, проектування використання канбанів Just In Time та планування, поліпшення якості, зменшення розміру партії та НЗП, а також поліпшення потоку. Нові дані процесу були взяті починаючи з місяця після впровадження. Ця затримка дала операторам машин можливість тренуватися і дістатися до нової системи компонування технологічного процесу.
З U-подібною конструкцією клітини; Деталі відповідають всім вимогам замовника. Таблиця в початковому процесі була видалена, майже виключивши НЗП. Зі зменшенням НЗВ і збільшенням виробництва.
Деякі концепції, що використовуються для вдосконалення процесу, включали загальну залученість працівників (TEI), менші розміри лотів, планування, інвентаризацію точок використання та покращений макет. Всі співробітники та керівники відділу були задіяні на всіх етапах проекту. Їхні ідеї та пропозиції були включені в процес планування та реалізації, щоб отримати більш широке сприйняття змін до процесу. Менші розміри партії були введені для мінімізації кількості деталей, виготовлених до виявлення дефектів. Були введені канбани (у вигляді стійок для обробки матеріалів) для контролю НЗП і реалізації тягової системи. І компонування клітин зменшило подорож між операціями.
Оператори були уповноважені зупиняти лінію, коли виникли проблеми. У вихідному стані оператори все ще продовжували запускати частини, коли операція не працювала. З канбаном
управління, розкладка виключила можливість зберігання WIP, вимагаючи від оператора відключення всієї лінії. Макет осередку надає відмінні можливості для поліпшення зв'язку між операторами про проблеми і коригування, для досягнення кращої якості.
Щоденна перевірка початкового стану процесу оператори витрачали багато часу або на очікування людини з обробки матеріалів, або виконуючи як обробку матеріалів. З U-подібною осередком доставка до місця використання більш краща для оператора. Коробки з сировиною оператор розміщує на шести рухомих роликових візках, куди легко дістати. Шість коробок достатньо, щоб тривати 24-годинний період.
Щоб скоротити час налаштування, інструменти, необхідні для ремонту та регулювання машин, розміщені в осередку. Гвинти не стандартизовані; інструменти налаштовуються в порядку збільшення розміру, щоб швидко визначити правильний інструмент.
Протягом трьох місяців процес контролювався, щоб переконатися, що він контролюється. Порівняння часових досліджень з початкового стану і реалізованої компонування продемонструвало збільшення обсягів виробництва з 300 до 514 готових виробів за зміну. Нова компоновка виключила подвійну обробку між другою та третьою операціями, а також на етапі упаковки. Це також зменшується протягом усього часу, полегшуючи цикл всіх чотирьох операцій у порядку витягування. Попит споживачів задовольнявся двома змінами, що зменшило вартість робочої сили.
Результати редизайну такі:
- Зниження НЗВ на 97%
- Виробництво збільшилося на 72%
- Брухт скоротився на 43%
- Використання машини збільшено на 50%
- Використання робочої сили збільшилося на 25%
- Витрати на робочу силу скоротилися на 33%
- Рівень сигми збільшено з 2,6 до 2,8
Цей проект дав зниження витрат на робочу силу та брухт, і дозволив організації зробити кращу роботу по здійсненню поставок вчасно, дозволяючи при цьому менший запас готової продукції. Щоденні показники виробництва та час циклу з однієї частини служили орієнтиром для моніторингу прогресу в досягненні мети. Незважаючи на підвищення рівня сигми, 43% зменшення дефектів, 97% скорочення НЗВ та збільшення виробництва на 72% сприяли досягненню мети проекту.
Впровадження lean - це нескінченний процес; це те, що безперервне вдосконалення - це все
про. Коли ви отримуєте один аспект lean реалізований, його завжди можна вдосконалити. Не зациклюйтеся на ньому, але не дозволяйте речам сповзати назад до вихідної точки. Завжди знайдеться час, щоб повернутися назад і вдосконалити деякі процеси.
Перш ніж Lean Manufacturing було впроваджено в Nypro Oregon Inc., ми працювали б з використанням традиційного Традиційне виробництво полягає у виробництві всього даного продукту для ринку, щоб ніколи не давати обладнання простоювати. Ці товари їх потрібно складати або відвантажувати замовнику, який може бути не готовий до них. Якщо виробляється більше, ніж можна продати, продукція буде продаватися з глибокою знижкою (часто збиток) або просто зламати. Це може додати до величезної кількості відходів. Після впровадження концепцій Lean Manufacturing наша компанія використовує якраз вчасно. Якраз вчасно стосується виробництва та доставки товару в кількості, необхідній, коли замовник цього вимагає, а не раніше. У бережливому виробництві виробництво виробляє лише те, що хоче замовник, коли він цього хоче. Це часто набагато більш економічно ефективний спосіб виробництва в порівнянні з високою ціною, великий обсяг обладнання.
Модульний тест:
1. Що таке 5S?
2. Будь ласка, поясніть кожен «S» з 5S.
3. Будь ласка, поясніть концепцію Кайдзен.
4. Що таке обробка Pull?
5. Що таке Пока-хомут?
6. Що таке шестисигма DMAIC?
7. Які цілі для нового технологічного компонування лінії виробництва труб?
8. Перш ніж вносити зміни, команда інженерів-виробників робить, що в першу чергу?
9. Будь ласка, перерахуйте результати редизайну.
10. Ключем до реалізації нової ідеї чи концепції є те, що робити?
ІНФОРМАЦІЯ ПРО ВІДНЕСЕННЯ ГЛАВИ
Ця глава була отримана з наступних джерел.
- Lean 5S, отриманий від Lean Manufacturing різними авторами, CC:BY-SA 3.0.
- Кайдзен отриманий на основі Кайдзен підходу до проектування стільникових виробничих систем: тематичне дослідження VirginiaTech, CC:BY-SA 4.0.
- Кайдзен (зображення), отриманий на основі Кайдзен підходу до проектування стільникових виробничих систем: тематичне дослідження VirginiaTech, CC:BY-SA 4.0.